The Indian automobile industry eclipsed Japan and Germany for the first time in January 2023 to become the third-largest auto market in the world. At the domestic level, the Indian auto industry is valued around USD 100 billion and contributes nearly 8% of the GDP. While auto manufacturers enjoy the limelight, manufacturers of auto parts like Uno Minda, Schaffler and Sundram Fasteners remain the underappreciated players, toiling away in relative anonymity.
The Nifty Auto index has given returns of 14.4% in the past 365 days till March 28, while the benchmark Nifty 50 gave returns of -1.6%. We don’t have a listed index for auto parts and OEMs, but Trendlyne’s auto parts & equipment industry has made returns of 22.7% in the past year.
Indian auto ancillary manufacturers bring springs, engine parts, suspension, shock absorbers, gears, headlights, axles, wiring systems, chassis, lights, batteries, pistons, brakes, bearings, wheels and air conditioning parts to the market. As of FY22, the Indian auto component industry has a market size of Rs 4,20,000 crore, with passenger vehicles (44%) and two-wheelers (22%) accounting for the major chunk.
The recent uptick in retail auto sales has put the limelight back on the auto industry. The sales which picked up in October and November 2022 due to the festive season have extended to 2023 as well. Retail sales in January and February 2023 have increased by 30% YoY.
Note: Revenues of top 50 listed auto part manufacturers
Higher price realizations driving revenue growth
The auto ancillary industry is a leading indicator for sales by auto manufacturers, as OEMs get orders before the actual sale of an automobile. India’s top 50 listed auto part manufacturers’ revenue on a trailing twelve months (TTM) basis is Rs 3 lakh crore as of Dec 2022 – a 16.6% YoY growth over December 2021 revenues. On a quarterly basis, revenue has gone up by 17% YoY.
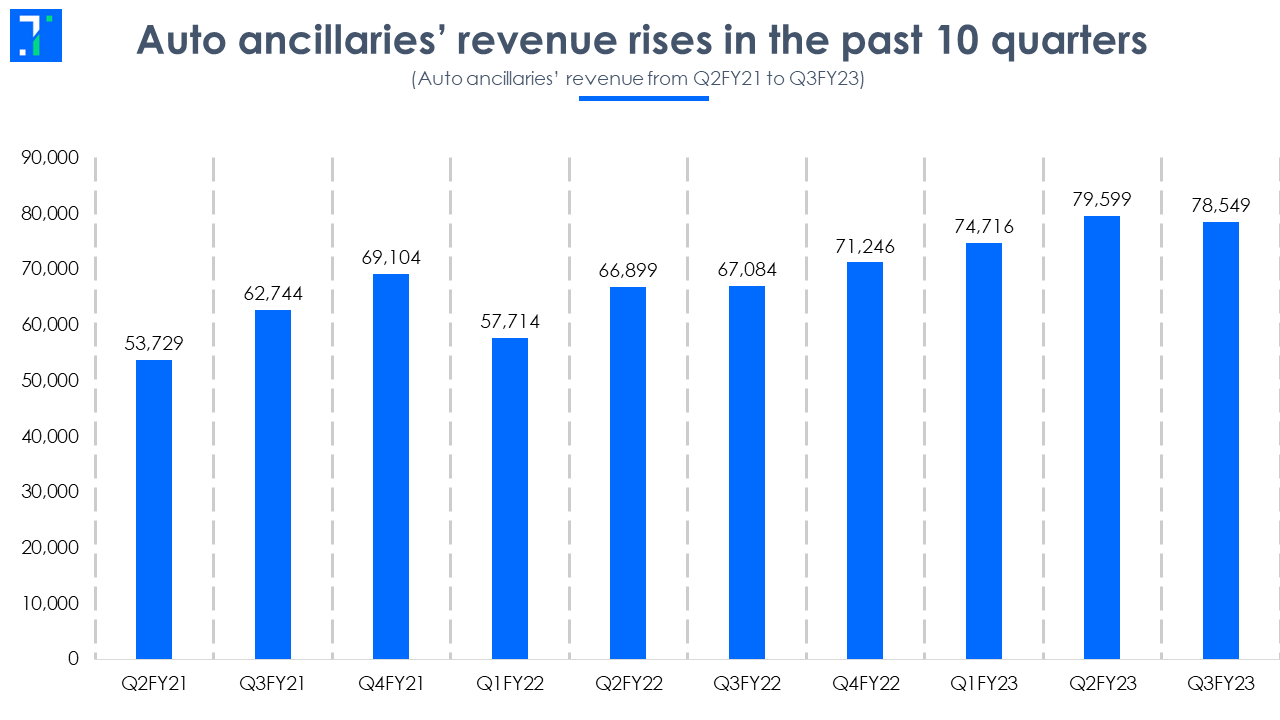
Note: Values in Rs crore. Cumulative revenue of the top 50 listed auto part manufacturers in terms of market capitalization.
Higher price realization by OEM manufacturers and rise in export-oriented products drove revenue growth. For instance, firms like Sundram Fasteners export a wide range of products to countries like China, Brazil, USA, UK and France. Most of the firms are not expecting FY23 growth in FY24. The volumes are expected to slow down and the growth is expected in the range of 6% to 7% in topline.
GNA Axles’ executive director Kulwin Seehra states that the revenue growth for the firm can be expected in the range of 7% to 8% on account of lower volumes.According to UNO Minda Chairman Nirmal K M, two-wheeler sales are not picking up as marketing is awaiting more EV-based products.
Opening up of China will soften raw material prices
Rising commodity prices and constraints in the supply chain have led auto OEMs to increase the price of manufactured components. The slowdown in China’s manufacturing sector caused supply chain issues starting from semiconductor chips to steel production and an increase in raw material prices at a global level. The opening up of Chinese economy might lead to demand revival of steel. In Q3FY23 steel prices have seen an uptick on account of higher consumption from China.
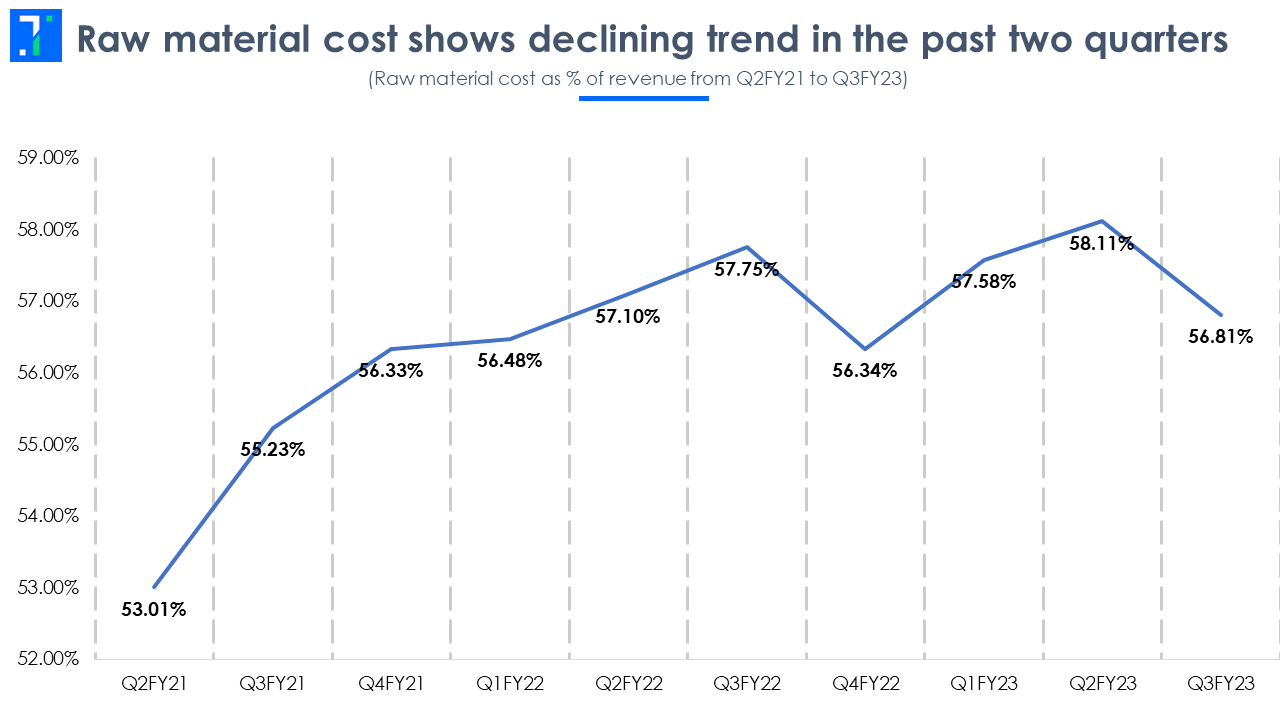
Indian auto part manufacturers’ plight is no different. The Indian auto part industry also saw its raw material cost increase. According to JSW Steel MD Seshgiri Rao, the upward movement of steel prices may halt and could even reverse in the coming weeks depending on China’s demand for steel consumption.
Note: Values in Rs/tonne
Due to its correlation with steel prices, the cost of raw materials has increased until Q1FY23. It saw a drop in Q2FY23 with steel prices. In Q4FY23, steel prices are still at elevated levels, impacting operating margins of auto part manufacturers.
Margin expand despite rising raw material costs
Margins of the auto part industry tell a different story compared to raw material costs. The margins have risen, mainly due to lower inventory levels and fixed costs. The past three quarters saw the highest automobile sales in India, leading to faster movement of inventory and better operating margins for auto part manufacturers. The increase in raw material cost was offset by higher pricing, lower inventory and lower fixed costs. According to a report by ICRA, freight costs increased by 4-5x in FY22 and have dropped by nearly half in CY23.
Margins are still below pre-pandemic levels but the increased volume has led to overall growth in the operating profits of the industry. Operating profits on a TTM basis for our sample size is Rs 33,013 crore (as of December 2022), a growth of 19.2% YoY
If we look at the bottom line, net profit margins have remained almost flat, in the range of 4.6% to 5.0% on account of higher interest expenses.
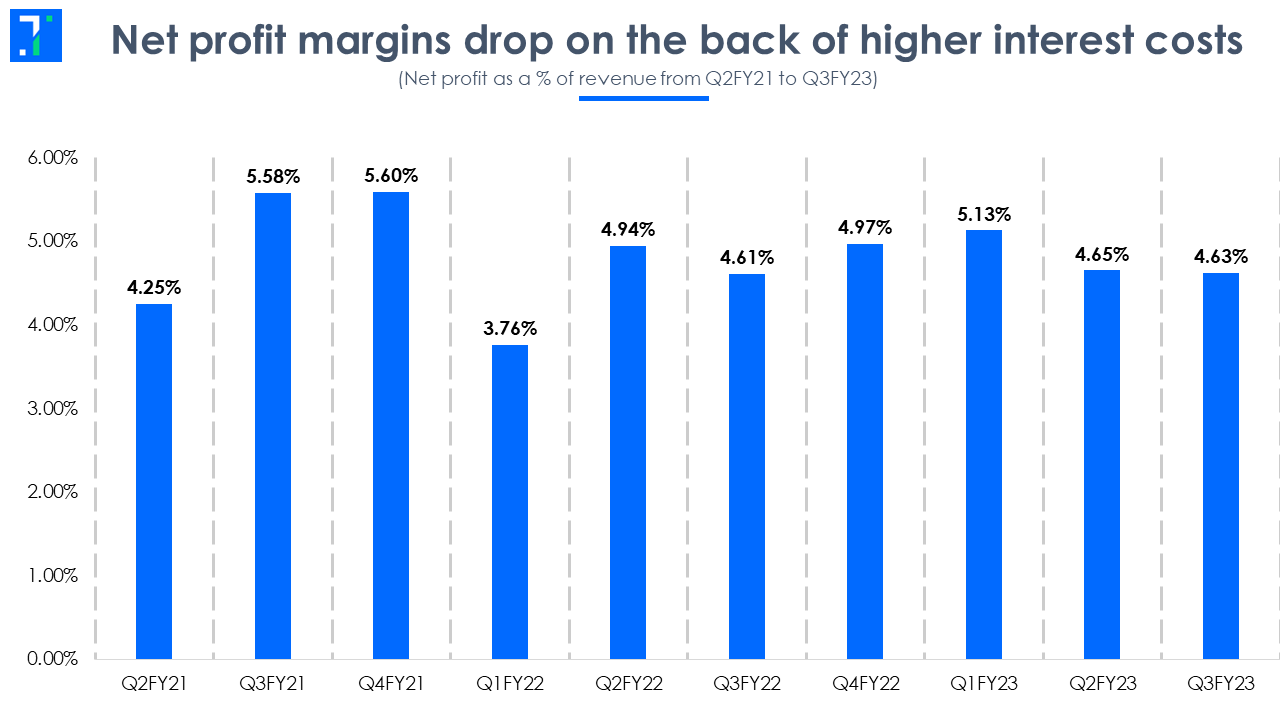
For instance, Samvardhana Motherson International has seen its finance costs increase 28% YoY for the trailing twelve months. Even with lower profit margins, the profitability of the sample size increased by 18% YoY on a TTM basis.
The top 50 auto part manufacturers generated profits of Rs 14,714 crore on a TTM basis. The amount might look small compared to bigger firms like Reliance Industries, whose Q3FY23 quarter profitability itself is Rs 15,792 crore. But the economic benefits of the auto part industry, and the growth outlook, are irreplaceable.
Export-Import of auto parts narrowing
India is a net exporter of auto components and accounts for nearly 34% of the auto component market. Europe, a major importer, buys nearly 30% of our exports. But India’s imports have recently been rising faster than exports. The import-export gap has been narrowing over the past couple of quarters as the demand for advanced components unavailable in India rises. Supply chain constraints and increased demand in Indian markets have also led to higher imports.
Note: Values in Rs crore. Source: commerce.gov.in
India sources nearly 30% of its auto components from China, and any supply chain disruption in China will adversely impact the auto component industry here. We have imported components worth Rs 48,834 crore in the past 12 months and exported for Rs 57,479 crore.
The global slowdown will impact Indian auto component manufacturers’ exports, hampering their profitability. However, the opening up of China’s economy is expected to offset this and soften the cost of raw materials, supported by reduced supply chain constraints.
Capex and PLI scheme to boost manufacturing in this industry
The auto ancillaries industry had not undertaken any capital expenditure (capex) during Covid times and hence, the pent-up demand post-Covid pushed companies to operate at higher capacity utilization. Change in technology with respect to EVs, sensors and assisted driving also proved to be challenging for Indian auto component manufacturers. These companies expect to see a capex of more than Rs 20,000 crore in FY24. This is expected to increase by 6% to 7% in FY25.
The Indian government has provided a capital outlay of Rs 26,000 crore for auto and auto component manufacturers under the PLI scheme. The scheme provides financial incentives to boost domestic manufacturing of Advanced Automotive Technology (AAT) products. As it focuses on technology, it covers firms with expertise in advanced driver assist systems (ADAS), battery development, sensors, telematics, collision avoidance system, etc.
For instance, Schaffler India plans to invest Rs 1,500 crore in capex for the next three years. According to Schaffler India MD Harsha Kadam, the firm is exploring the possibilities to take benefit of PLI schemes in electric vehicle technology (motor or ECU) and hydrogen fuel cell development.
Incentives for the companies vary from 13% to 15% on the determined sales value of the firm. This will provide a much-needed boost to auto OEMs.