India’s chemical industry today is at a crossroads – on one side, the weather has turned unpredictable, with thunderstorms and dry patches coming unexpectedly, and the El Nino driving temperatures up worldwide. This has taken a toll on agrochemical consumption.
On the other side, the reopening of Chinese chemical manufacturing has resulted in cheaper imports to India, putting pressure on prices for domestic producers. The global economic slowdown has only added to the pain. The unfavorable conditions have contributed to lower exports of specialty chemicals from India and hit chemical stocks.
India’s chemical industry constitutes 7% of the country’s GDP and has a market size of $240 billion. India’s Index of Industrial Production (IIP) has grown by 0.6% since April 2023 but the chemical sector has not matched this trend, contracting by 2.1% during the same period.
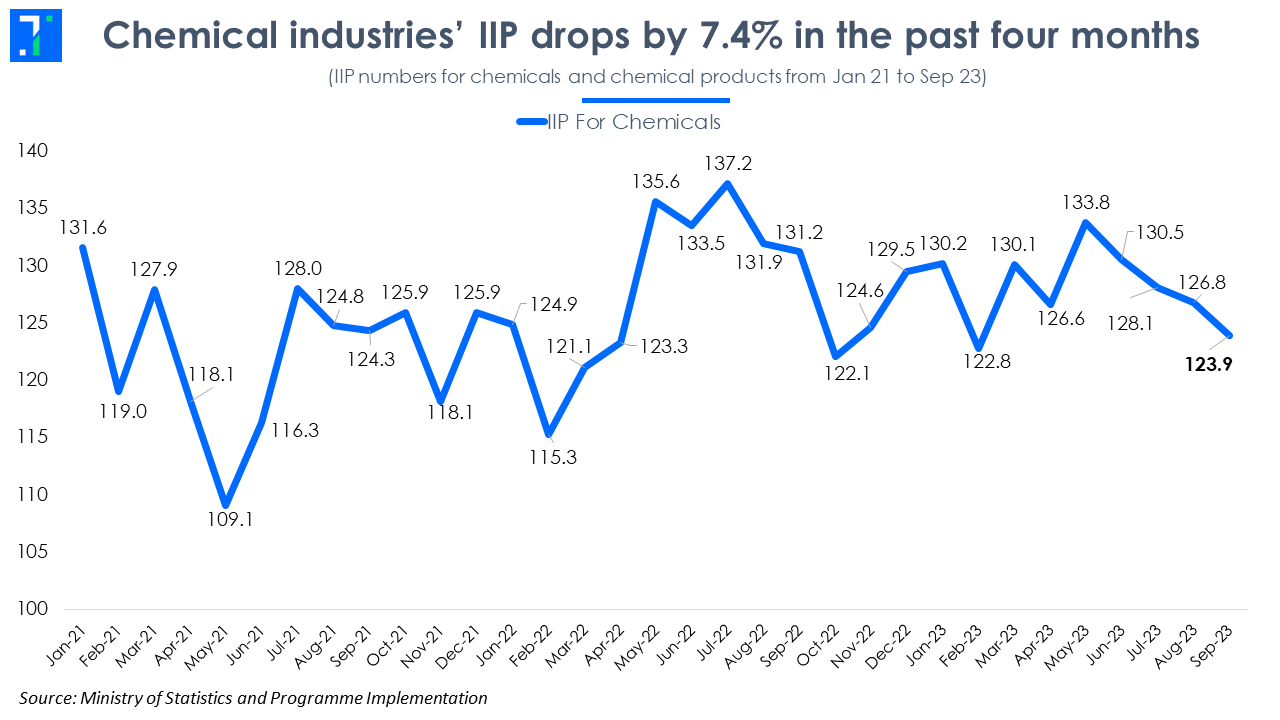
Chemical industry’s IIP drops by 7.4% in the past four months
The first half of FY24 saw a drop in production volumes as dealers and end-users had higher inventory. Chemical manufacturers have also struggled with margin pressures due to high-priced inventory impacting profitability. This problem is likely to persist till the end of FY24. However, contract manufacturers and export-oriented producers should recover faster than their industry peers.
Chinese dumping has affected Indian manufacturers
The Chinese chemical industry, whose production exceeds domestic demands, has turned its focus to exports. Countries like India, with significant demand for chemicals, are among its favoured destinations. But this is creating pricing pressures for Indian manufacturers.
India's chemical sector is traditionally a net importer, resulting in a trade deficit. But it has been a net exporter of dyes and intermediates. However, for the first time in 22 months, India has become a net importer in this segment too. Low-cost imports from China have resulted in end-manufacturers preferring these over pricier Indian alternatives.
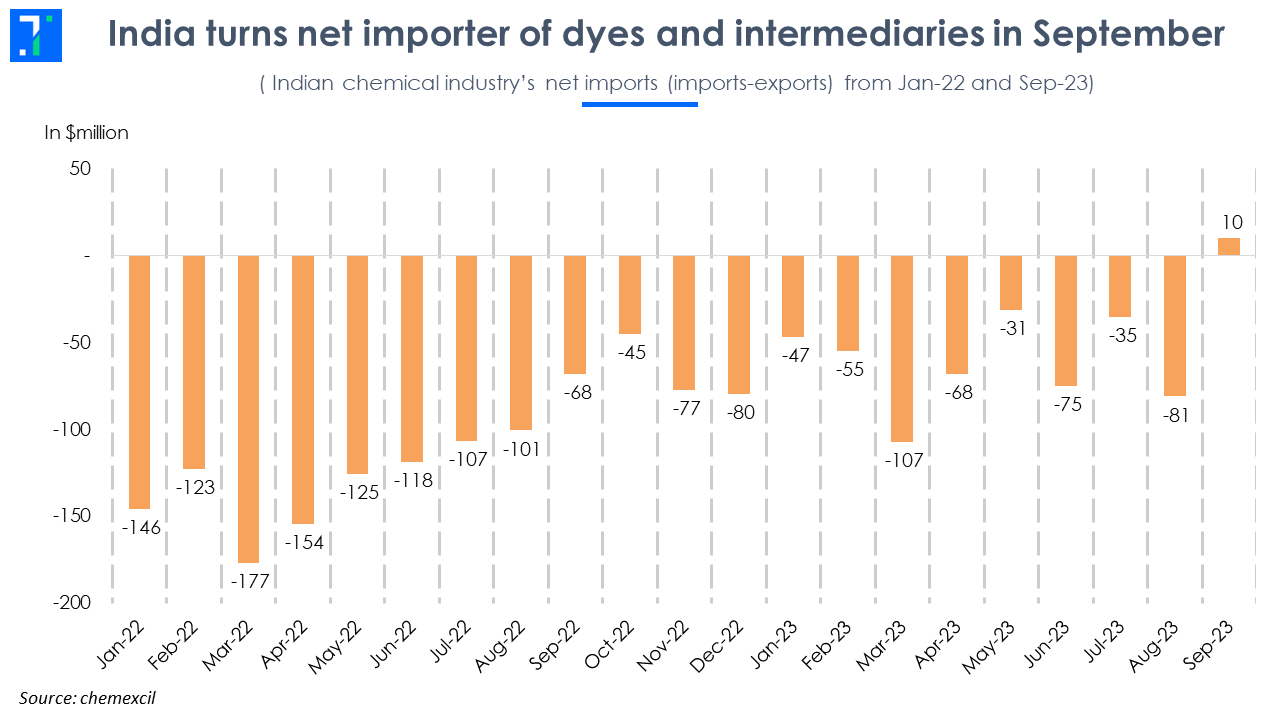
India turns net importer of dyes and intermediates in September
Indian companies rely on China for their raw material needs. Often, imported finished chemicals from China are cheaper than domestic products. According to Manish Kiri, MD of Kiri Industries, Benzene prices in India are around $920 per tonne, whereas Aniline (which uses Benzene as raw material) is sold for $1,700 per tonne. In contrast, Chinese Aniline comes at $1,400. This kind of competition makes the Indian business unviable.
Raw material prices increased in September owing to planned shutdowns in China for the seven-day Golden Week holiday. However, prices dropped again as Chinese capacities resumed.
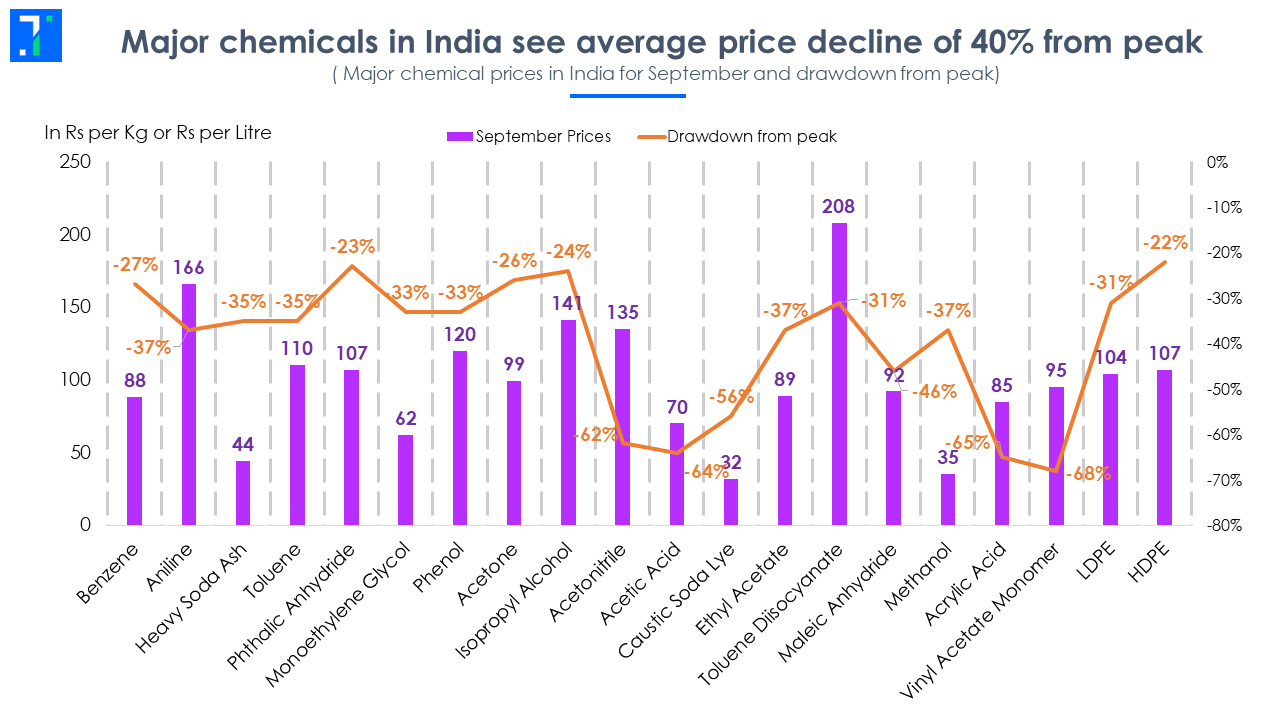
Major chemicals in India see average price decline of 40% from peak
The prices of major chemicals sold in India have corrected by around 40% from their peak, impacting margins.. As a result, manufacturers are resorting to lower sales rather than cutting their prices in line with Chinese competition.
Margin pressure compromises revenue growth
The chemical industry has faced many challenges over the past two quarters, marked by a 13.9% YoY degrowth in Q2FY24. This decline was on account of lower volumes and lower price realisations. A stock buildup among Indian consumers in H2FY23 led to lower volume offtake in H1FY24.
For instance, UPL reported a 7% decline in volumes and a 15% drop in price realisations, driven by the availability of cheaper Chinese chemicals in the market. Also, the Indian agrochemical sector was affected by delayed rainfall, resulting in reduced consumption of chemicals during the quarter.
Only a few specialty chemical manufacturers like Rossari Biotech, Neogen Chemicals, Navin Fluorine and Sudarshan Chemicals were able to achieve positive YoY growth in the quarter.

Operating profits in chemical industry remain below Q4FY23 levels
Note: This data includes consolidated earnings of 19 listed companies: SRF, Galaxy Surfactants, Rossari Biotech, Sudarshan Chemicals, Atul Ltd, Vinati Organics, Navin Fluorine, Supreme Petrochem, Balaji Amines, Anupam Rasayan, UPL, Aarti Industries, Deepak Nitrite, Neogen Chemicals, NOCIL, Gujarat Alkali, Sumitomo Chemicals, Tata Chemicals and Fine Organics
The industry has also been grappling with shrinking profit margins. Net profit margins have dropped from 9.6% in Q2FY23 to 5.4% in Q2FY24. The margin hit was due to high-cost inventory and a lack of pricing power. While the specialty chemicals segment has benefited from a stronger dollar due to exports, the overall industry has been impacted by pricing issues.
Chinese chemicals are being dumped in India at a 20-25% discount, while Indian manufacturers have only reduced their prices by 10-15%. This disparity has led to lower volumes but limited the margin hit.
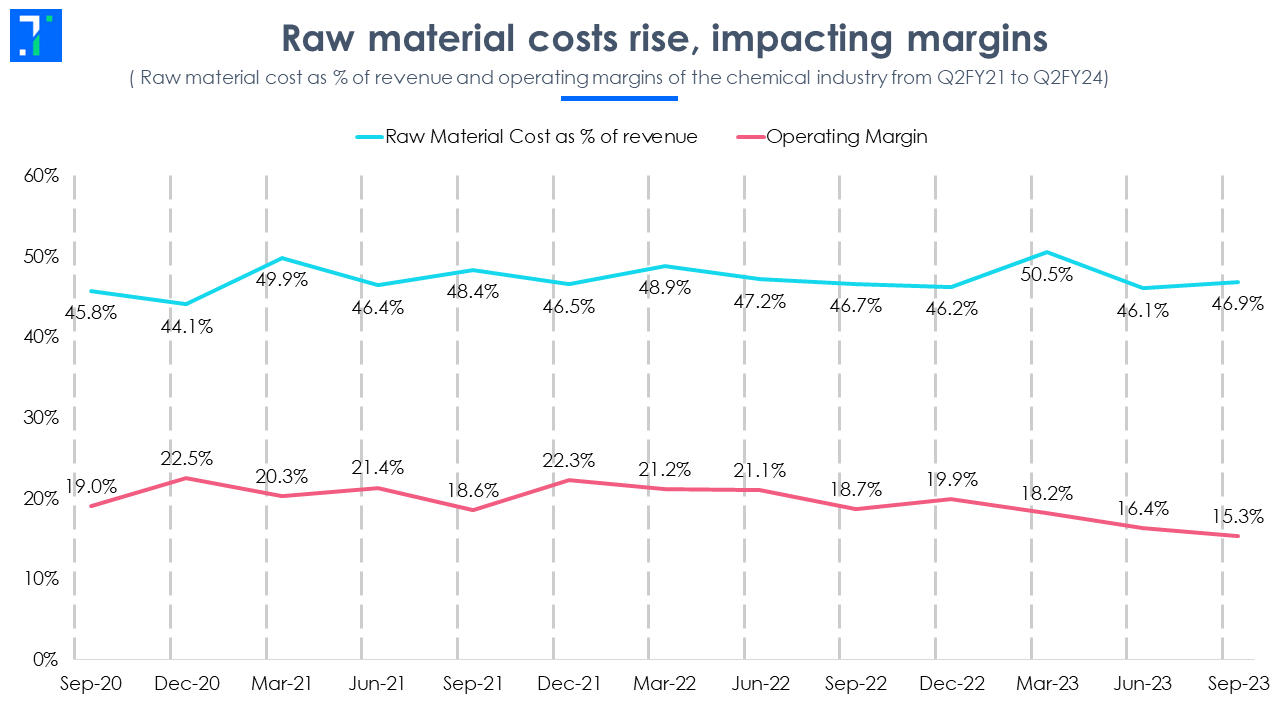
Raw material costs rise, impacting margins
Currently, chemical manufacturers are focused on destocking their high-cost inventory. Even with the drop in raw material prices, the existing high-cost inventory has resulted in lower margins for manufacturers. This is evident in the declining cost of raw materials as a percentage of revenue and contracting operating margins.
Industry seeks government support amid global pressures
The chemical industry is looking for support from the government to impose import duties on Chinese chemicals. However, the government has yet to act on this request as the price of these commodities directly impacts the agriculture and pharmaceutical industries.
Recessionary fears in key markets like Europe and the US, and higher output from China continue to pressure Indian exports. Even chemicals supplied to pharmaceutical APIs (Active Pharmaceutical Ingredients) are facing pricing pressure.
At this point, Indian chemical manufacturers are unable to benefit from domestic demand. However, once the Chinese imports slow down, specialty chemicals and export-oriented manufacturers will recover faster than the industry